For over 4 decades Quadro has been refining and improving conical milling equipment and technology. It has become one of the most common methods used for powder processing in the pharmaceutical, chemical and food industries for size reduction, deagglomeration and delumping.
Due to these years of experience, we have the largest selection of conical screens and impellers and the widest impeller RPM range of any comparable conical mill. This means that Quadro is able to help customers to achieve their target PSDs and improve milling capacity without changing the base model.
Today, there are two distinct conical mill designs:
- The Overdriven Comil®
- The Underdriven Comil®
What is the difference between Overdriven and Underdriven?
The Overdriven Comil®
The original cone mill was invented by Quadro® in 1976. It consists of a cone-shaped mill screen with an impeller that is vertically mounted and driven from the top by a direct drive belt.
The hand-fed product falls through the infeed into the conical screen chamber where the rotating impeller imparts a vortex flow pattern to the incoming material. This material is forced to the screen surface by centrifugal acceleration ensuring continuous delivery into the ‘action zone’ between the screen and impeller.
Here the material is sheared through the screen, thereby creating a uniform particle size reduction which is then discharged through the screen openings. The finished product is discharged at the bottom of the milling chamber.
The Underdriven Comil
comprises the same cone-shaped mill screen, but here the impeller is rotated and driven from the bottom by a sealed gearbox. When the gearbox design was patented in the early 1990s by Quadro Engineering, it revolutionized the industry by offering a much more compact design that was ideally suited for integration with upstream and downstream equipment.
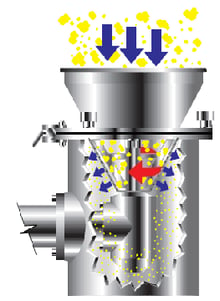
Although the same milling process applies as the Overdriven, with material entering via the infeed and being forced to the screen surface by centrifugal acceleration, the benefits of a compact design are numerous.
For example, the overall height was reduced by over 30%, making it a lot easier to install in tight spaces. Another benefit is that with an in-line design, the infeed opening is approximately 20% larger, which can result in a significant increase in capacity (in Overdriven mills, there is an off-set entry point that reduces the product’s effective inlet diameter).
Because the Underdriven Comil® is so much more compact than its Overdriven counterpart, it is ideal in situations where mills need to be installed on height-adjustable lifts or columns, or inside an isolator for added containment (in this situation the motor is installed outside the isolator, keeping the mechanical components apart from the product, which is not feasible with a belt-style Overdriven machine).
Choosing the right conical mill and screen
Deciding that conical milling is the right type of milling methodology for your own business will depend on the material being processed, the target particle size and PSD and the production capacity needed.
Keeping in mind that particle sizes are achieved by selecting the right conical screen hole type & size, impeller arm profile, and tip speed, cone milling is particularly suited to achieving particle ranges from 4750 microns to 250 microns with tight PSDs – download our particle sizing card for more information.
With the right model selection, they can deliver very high capacities for such a small footprint, and due to the low residence time in the mill, they are suitable for many heat-sensitive products.
Deciding between Underdriven and Overdriven cone mills is really a matter of how the mill will be integrated into the main process.
If the application is simple and straightforward, where high kgs/hour is required and there is a lot of available space, then an Overdriven model may be the most logical choice. Whereas, if the mill needs to be coupled upstream/downstream in tighter spaces, or it needs to be attached to a lift or a wall or to an isolator, then the Underdriven model is the better choice.
A major benefit of the Underdriven design is its flexibility to allow the milling head (or chamber) to be easily removed from the spindle/motor, for instance for cleaning or preventive maintenance. This is because the driving mechanism is contained within the gearbox.
With the Overdriven models, because they are belt-driven and the impeller is driven from above, there is no opportunity to separate the milling chamber from the rest of the machine.
This head-removable feature is the foundation for a new series of lab and production-sized milling platforms that are revolutionizing how customers plan their investments and improve their powder processing efficiencies.
How is this done? Simple. Because milling heads can be easily removed from their drive/motor, it opens the door for flexible milling platforms where a user can have three or four separate milling heads, but only need one single drive platform. Then, when a milling head is installed via the sanitary clamp connection, the system auto-recognizes the technology and sets the operating impeller speeds accordingly.
Perfect examples of this great advancement can be found in Quadro’s SLS and SDx exchangeable head platforms.
What are the benefits of a Comil?
Whether you choose the Overdriven or the Underdriven Comil® they both offer the benefits of:
- Scalability
- Low RPM
- Low Energy operation
- Low Noise generation improves the operating environment
- 360o Discharge
- Choke/Flood Feed
- Low Dust generation
- Uniform Particle Size Distribution
- High Capacity with Small Footprint
- No Metal-to-Metal Contact
- Easy/Fast Clean Design
Typical Applications for the Quadro Comil
The Comil® is a versatile mill and is used across a wide range of applications in a multitude of situations:
- In wet granulation conditioning
- Dry milling for final sizing of pharmaceutical powders
- integrated inside isolators to increase containment levels
- coupled to vacuum transfer systems
How can we help?
If you would like to know which Quadro Milling and Powder Processing Technology are right for your application, then contact us and one of our experienced application team will get in touch.
Topics:
Milling