Brief history of Lean Manufacturing
Global manufacturing has steadily evolved from craft to mass production. Preceding the middle of the 20th century, standard hallmarks of mass production were large inventory stocks, long production lines with thousands of low-skilled assembly workers, and huge amounts of diversified waste.
Various production strategies were designed and applied by companies to increase their return on investment, but none were as successful as Toyota in Japan. In the middle of the 20th century—during Japan’s regrowth after the 2nd World War—Toyota pioneered lean manufacturing principles through the application of the work of Dr. Edward Deming.
Deming had been sent to Japan in 1946 by the Economic and Scientific Section of the War Department to study production issues in the war-damaged nation. Deming influenced a group of Japanese industrial managers in correcting serious and persistent quality problems. After teaching them statistical methodology and by inspiring confidence, Deming was convinced that the Japanese would capture the world market within five years if they followed his advice.
“They beat my prediction,” said Deming. “I had said it would need five years. It took four.”
In particular, the successful changes adopted by Toyota were studied by many others and a new manufacturing methodology and production strategy was identified that would forever change the way business leaders would think about their products, their employees, and their customers. This became widely known as the Toyota Production System (TPS).
Basic principles of Lean manufacturing
The TPS system was really the originator of the generic process management philosophy now known as Lean. James Womack, in his book entitled Lean Thinking1, explained the five basic principles of Lean Manufacturing:
Understanding Customer Value. Only what your customers perceive as value, is important.
Value Stream Analysis. Once you understand the value that you deliver to your customers, you need to analyze all the steps in your business processes to determine which ones actually did add value.
Flow. Instead of moving the product from one work zone to the next in large batches, production should flow continuously from raw materials to finished goods in dedicated production cells.
Pull. Rather than building goods to stock, customer demand pulls finished goods through the system. Work is not performed unless the part is required downstream.
Perfection. As you eliminate waste from your processes and flow product continuously according to the demands of your customers, you will realize that there is no end to reducing time, cost, space, mistakes and effort.
The National Institute of Standards and Technology Manufacturing Extension Partnership’s Lean Network summarizes the definition of Lean Manufacturing as:
A systematic approach to identifying and eliminating waste through continuous improvement, flowing the product at the pull of the customer in pursuit of perfection2.
Why is Lean manufacturing so effective?
Once properly adopted by a manufacturing firm, Lean principles can improve efficiency, reduce waste, and increase overall productivity. Companies can then benefit from improved product quality, reductions in wasted resources, improved quality control and better overall management of manufacturing workflows while maximizing customer value.
Lean manufacturing is a journey toward continuous improvement. Adopters never arrive at a destination as such, because they are reprogrammed to continually look for ways to improve processes. Even after major improvements have been made and savings have been validated, companies still need to look for ways to become more efficient. Every employee makes a commitment to pay attention and analyse everything, cut down on waste and increase efficiencies. Lean is a continuous, intentional practice that is constantly developed and evolved across an entire organization.
Reducing waste with Lean principles
There are eight types of waste identified in lean manufacturing easily remembered by the acronym D.O.W.N.T.I.M.E. which stands for Defects, Overproduction, Waiting, Non-utilization of talent, Transportation, Inventory excess, Motion, and Excess processing.
By identifying and cutting waste from the above categories, companies can save time and money running their businesses.
The Lean building blocks
Jerry Kilpatrick in his paper on Lean Principles2 identifies common tools or Lean Building Blocks that are available to manufacturers.
While any of these may be implemented as standalone programs, the true impact on the bottom line will only come when several tools are implemented in the proper sequence. Kilpatrick describes the tools as follows:
- Pull system. Producing product at customer demand.
- Method for maintaining an orderly flow of material.
- Work cells. Arranging operations and/or people in a cell vs. a line.
- Total productive maintenance. Co-operative maintenance methodology to optimize machine performance.
- Total quality management. Continuously improving all areas of a company’s operation.
- Point-of-Use-Storage. Cutting down on excess movement of people and materials.
- Quick changeover. Reducing the amount of time to change a process from producing one specific type of product to another.
- Batch size reduction. Reduced batch sizes shorten the overall production cycle which enables companies to deliver more quickly and invoice sooner.
- 5S or Workplace Organization. Systematic method for organizing and standardizing the workplace.
- Visual controls. Simple signals that provide an immediate and readily apparent understanding of a condition or situation.
- Concurrent engineering. Using cross functional teams to develop and bring new products to market.
Enabling a Lean workflow with process equipment from IDEX MPT
With the ability to work with a wide variety of materials (solid, semi-solid, and liquid), IDEX MPT provides process equipment and global support service solutions that enable processors around the world to achieve consistent, repeatable results when producing product for their end users.
IDEX MPT is a division of IDEX Corporation and is comprised of four companies specializing in the processing and handling of powders, particles and fluids: Quadro Engineering; Fitzpatrick Company; Matcon; and Microfluidics International.
Milling and powder processing technologies from Quadro and Fitzpatrick
Quadro Engineering developed the original Comil® in 1976, and the Comil® has since evolved into the global processing standard. Quadro is now the trusted partner of the world’s leading pharmaceutical, food and chemical processing companies.
For over 80 years, the Fitzpatrick Company has built a reputation based on technological evolution in both design and manufacturing. The product lines from Quadro and Fitzpatrick allow processors to adopt more thorough Lean manufacturing principles into their workflows.
Quadro’s range of Milling and Particle Sizing Equipment enables the achievement of tight particle size distributions in dry and wet milling applications. Quadro offers products that enable conical milling and screening, Fitzpatrick hammer milling technology, all of which are available from lab scale up to full production scale for applications including OSD and API pharmaceuticals, nutraceuticals, food and chemical.
Quadro and Fitzpatrick's portable milling and screening systems combine complete, controlled recipe-driven processing environments that can be moved from station to station helping to decrease overall plant maintenance costs and save wasted floor space. Quadro and Fitzpatrick equipment can be configured to meet optimal process layout in marginal spaces, minimizing product transportation and decreasing labor costs.
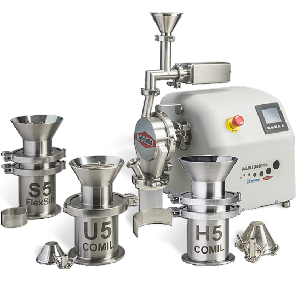
Quadro and Fitzpatrick equipment is designed with few parts and no entrapment areas to reduce the risk of cross contamination and ease of cleaning and maintenance. Visual controls and a recipe driven HMI allow for simple, repeatable operability.
Quadro and Fitzpatrick's product lines can be incorporated seamlessly with Matcon IBC Technology for the most efficient, Lean manufacturing workflow.
Dry granulation processing with Fitzpatrick
Dry granulation is the leanest, efficient method for conditioning powders. Compared to wet granulation it uses less equipment and processing steps and is unlikely to damage the ingredients.
Dry Granulation is a continuous manufacturing process that removes the need to spend time constructing the correct batch sizes. With fewer process variables it is simpler to validate, optimize and scale—a truly Lean approach.
Dry granulation by roll compaction is the process of compacting primary particles into larger granules in order to:
- Lock in blend ratios. Prevent segregation later in the manufacturing process.
- Improve powder flow. Conveying and feeding into downstream processes are now trouble-free eliminating caking and bridging.
- Better control dissolution. Create granular material that will dissolve or disperse more effectively.
- Densify materials. Reduce bulk density during storage, transport and packing, reducing wasted space.
- Control dust. Reduce wasted product, cross contamination and environmental risk.
Powder handling systems from Matcon
Using the Matcon IBC method of manufacturing, shorter runs can be produced as changeovers are quicker and simpler. This means you can make-to-order with smaller inventory levels and minimal wash-in-place (WIP).
The decoupled nature of the Matcon IBC system gives total flexibility and the agility to respond rapidly to changing customer needs and directly reflects many of the building blocks of the Lean system.
Decoupling allows for parallel processing of each step so that formulation, blending, packing and cleaning can all take place simultaneously. IBCs are used to transport material between manufacturing steps, which means each step is independent. One recipe can be packed, at the same time as one is being blended and another being formulated, whilst the used IBCs are cleaned.
With Matcon IBC systems there is no waiting at the blending stage. IBC containers are filled off-line and since they are also the blending vessel, they are loaded on and off the blender immediately. As soon as one IBC is removed the blender is ready to receive the next prepared container. No cleaning is required between batches or recipe changes.
Matcon incorporates Quadro’s product line for inline milling and screening capabilities as part of the efficient, Lean manufacturing workflow.
Scalable batch production with Microfluidics
Microfluidics manufacture laboratory and commercial processing equipment used in the production of micro- and nano-scale material industries including pharmaceutical, biotechnology and diverse industrial applications including chemical, vaccines, energy, cosmetics and nutraceuticals/foods.
Microfluidizer® Processor High Shear Homogenisers high shear fluid processors enable manufacturers to develop very small amounts of product during R&D and easily scale up to larger batch requirements retaining remarkably uniform particle size distributions throughout.
The Microfluidics range of homogenizers enables manufacturers to incorporate several of the Lean manufacturing building blocks into their workflows including make-to-order capabilities, production flexibility and reduced production inventory.
Solutions from IDEX MPT can improve your Lean manufacturing
The product managers, sales engineers and aftermarket teams across the IDEX MPT group want to help you improve your processing workflows and join you on your journey toward continuous improvement. To help further explain how we might be able to help you, please get in touch with us for a free consultation.
Notes:
- Womack, James P. and Daniel. T Jones, Lean Thinking, Simon and Schuster, New York, NY, 1996
- Jerry Kilpatrick, Lean Principles, Utah Manufacturing Extension Partnership, 2003